Managing, controlling quality and compliance within your ERP system, or using a different database seems like a no-brainer. Nonetheless, there are still many manufacturers who are still using a different system to oversee and track quality, compliance, and in some cases lots/batches as a result of their manufacturing. If you have a Quality Management System within your ERP, why wouldn’t you utilize it?
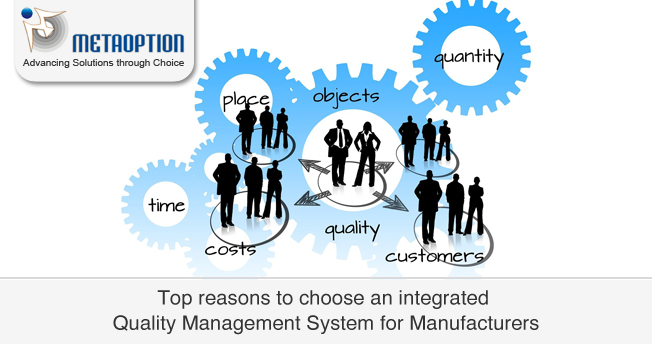
Meta Quality Control (QC), an ERP System integrated with Microsoft Dynamics 365 Business Central and NAV manage your production, entire quality process, capture test results, create rework orders and regulate stock to ensure faulty products don’t make it out of the warehouse.
End to End Quality Control is the way to Compliance
There are various advantages to utilizing your ERPs quality system or having a truly integrated Quality Management System. Wouldn’t it be incredible to be able to easily do the following list by integrating them into your purchase, production, and trace back to your customers?
Here are the top reasons to choose Meta Quality Control (QC) for your business:
Keep track of seller performance
- Track and test inbound raw materials
- Ensure raw materials have to tested before they hit production
- Lot tracing if required back to the seller
Automatically determine sample size
- Calculation based on the Acceptable Quality Levels method where the results of the sample inspection are applied to the complete lot
Evaluate manufacturing processes and customer satisfaction
- Inspect the raw materials before and during specified quality control during production and the finished good
- Final check of the quality if desired before transportation to the customer to ensure complete customer satisfaction
- Generate/Print/Email certificate of analysis (COA) reports and show them attached to the customer shipment
- Report on deviations and create corrective activity reports with an audit trail
Automatic data snapshots
- Use Business Integration Solutions to make snapshots of the data at measurement time
Maintain standards compliance and audits for your industry such as ISO, GMP, and FDA
- Generate and maintain inspection plans, checklists, etc. and track these records
- Keep up with non-conformances with a complete audit trail
User-definable check sheets
- Create Questions and Answers to be completed at measurement time. Set target values to determine Accepted or Rejected
Ease your traceability steps for recalls and audits
- Quickly get the information that is require from raw material lot numbers and QC results all the way to finished goods tracking. That’s what you can get from a fully integrated QMS
- It’s time for your ISO or GMP audits? They will be a breeze since everything is in one spot including QC tests, agendas, and documentation attached to your processes within production, purchasing, and so on
To know more reasons and more information about Meta Quality Control (QC), contact us today at MetaOption.