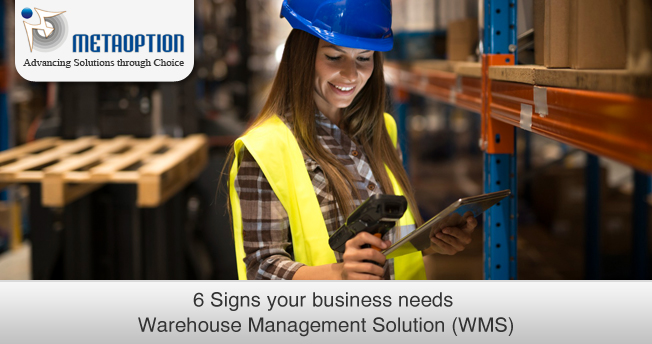
Every warehouse manager feels pressure to operate their facility at top capacity with low overhead. It’s often difficult to keep up with the latest trends due to the rapid changes being made to the industry by advances in technology. Failing to stay on top of warehouse management best practices puts your business at risk of getting left behind by your competition. Following current best practices has become even more important in the face of global supply chain disruptions caused by the COVID-19 pandemic. Costumers today expect that orders will consistently ship the same day, without mistakes or any wrong items. As a result, small to medium-size businesses (SMBs) should be concerned about if the performance of their business is being impacted due to the lack of a Warehouse Management System (WMS).
If you’re looking to streamline your existing processes and look for opportunities to maximize productivity, MetaWMS – Advanced Warehouse Management System helps you to improve warehouse efficiency & productivity with the integration of Dynamics 365 Business Central. When does a business know it needs Warehouse Management software?
The following are six signs that help to know your business needs a warehouse management system (WMS):
Warehouse Is Running Out of Space
Whenever your products are growing out of their space, your first thought may be to move to a larger warehouse. Moving can be costly to both your budget and timelines. An efficient warehouse may not need more space to operate. WMS can optimize your workflow so that you produce more from the same space, even as the business grows.
Disorganized Warehouse
A chaotic space impedes workflow. You run the risk of damaging or misplacing your stock and putting your workers’ safety at risk. Employees need to know where all the products are and be able to create the best pick route. WMS will help you arrange your stock in a way that works best for productivity and safety.
Use of Spreadsheet to Track Inventory
In a small company with a low number of inventory items, it is possible to keep track of your stock in a spreadsheet. For a larger company that has a lot of items, this system is inefficient. Spreadsheets are difficult to update and cannot reflect the live inventory counts. A WMS can automate this process, so you can see how much you have and where it’s going in real-time. Your workers will be able to spend more time doing their tasks and not updating cells in a spreadsheet.
Items are Often Out of Stock
In case your company isn’t able to forecast its sales, the warehouse may not be able to meet demand. A high number of out-of-stock products reflects poorly on your business. Plus, backlogging orders slow down the warehouse’s productivity when it’s continually trying to catch up instead of working with the flow. WMS systems come with tools to help you forecast sales and manage your channels. These tools will help your warehouse get the quantities it needs for every item.
Delay in Deliveries
If your warehouse is in chaos, it will take your workers longer to assemble an accurate order. This may mean that orders are shipped late, or your company has to spend more time expediting to get products to the customer on time. A WMS software solution will streamline workflow, help orders get fulfilled on time, and deliver invoices.
Warehouse Inefficiency Constraining Company Growth
As other areas of your business grow, your warehouse needs to keep up. Any delays in the warehouse will keep your business from increasing its market reach and profit. Productivity is especially crucial during your peak seasons, where the potential for maximum revenue is high. Locate your inefficient areas and processes, solve these issues and work in tandem with company demands using WMS software.
Your warehouse should work with the flow of your business model. MetaWMS, a warehouse management system will help you keep everything on track to stimulate business growth and increase your profits.
For more information and a tailored demonstration contact us today at MetaOption.